Ege carpets production tour Brad Turner. October 24, 2015.
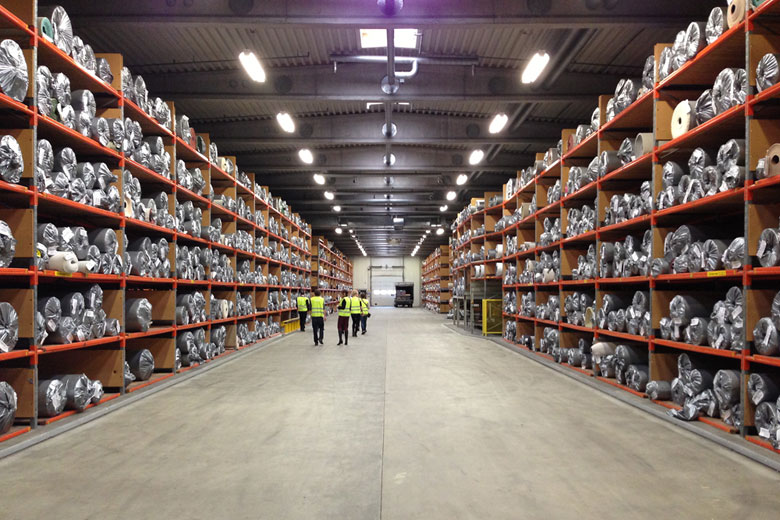
Materials Council visited the central Herning factory of Danish carpet brand Ege, one of Europe’s largest carpet manufacturers, to see first-hand the advanced technology employed in the production of their carpets.
Founded in 1938, Ege design, develop and manufacture high-quality pure wool and blended wool and polyamide (nylon) carpets, primarily for the contract market. Annually they produce around 5 million m2 of carpet.
Ege’s advanced manufacturing facilities at their factory in Herning allow them to produce a range of carpet products in the industry’s shortest lead time, including completely custom designed broad loom with relatively small minimum quantity requirements of 40m2. A large selection of Ege’s standard patterns can also be ‘recoloured’ allowing customers to specify a customised design more affordably.
Ege believe that to lead the contract market they must address the unique demands of each professional customer which they do so through a high level of service and an attitude of collaborative design and production for each of their clients’ projects. From their in-house design and colouring teams to their highly flexible production facilities, Ege work closely with their client from project initiation right through to installation to ensure the result is as the designer intended.
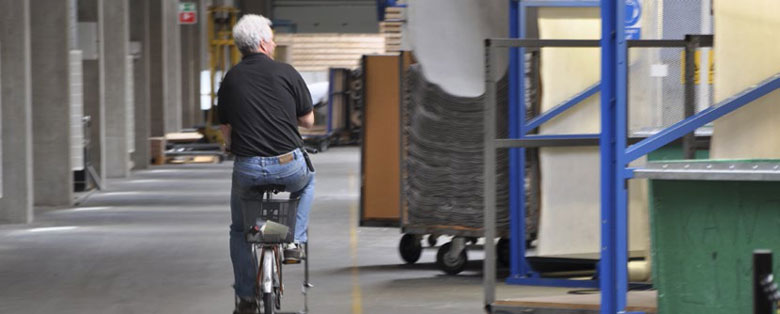
Ege also have excellent technical data available and literature communicating and documenting how they address issues such as sustainability and corporate social responsibility, demonstrating their commitment to openness and progress in these areas and also making it easy to obtain the required data, information and certification when considering and specifying their products.
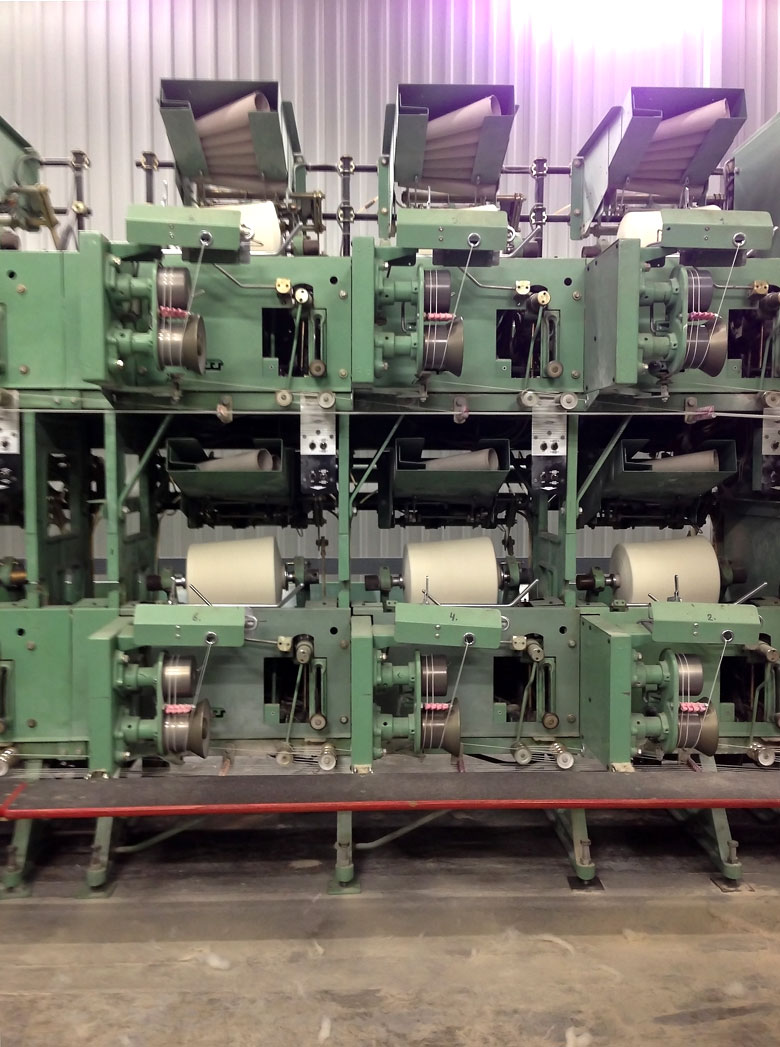
Production
At Herning, Ege employs a 70m long ‘Twistset’ system (one of only three in Europe), a continuous yarn processing system that produces the yarn used for Ege’s signature Highline 80/20 collection (80% wool, 20% polyamide), a velvet-style cut pile carpet.
The woollen fibres are scoured, washed, mixed with other fibres (such as synthetic Antron polyamide and antistatic carbon fibre), twisted, set and moth-proofed before the blended yarn is dried and wound back on to cones.
Ege use high-quality wool sourced from New Zealand and the UK, as opposed to lower quality Chinese wool, which is whiter in appearance and has longer fibres producing a stronger yarn and guarantees very low piling in the finished carpet.
The Twistset system manufactures two-ply yarn with more turns than other systems producing carpet with a more uniform texture and very upright and erect pile. By setting and drying the yarn at lower temperatures than other production methods the Twistset system ensures there is no yellowing of the yarn, creating more vibrant colours in the final dyed carpet.

At the Herning facility carpets are manufactured from both pre-dyed and natural white un-dyed yarns produced by the Twistset system. Carpets made of natural white un-dyed yarns are dyed on a computerised dyeing system called the Millitron.
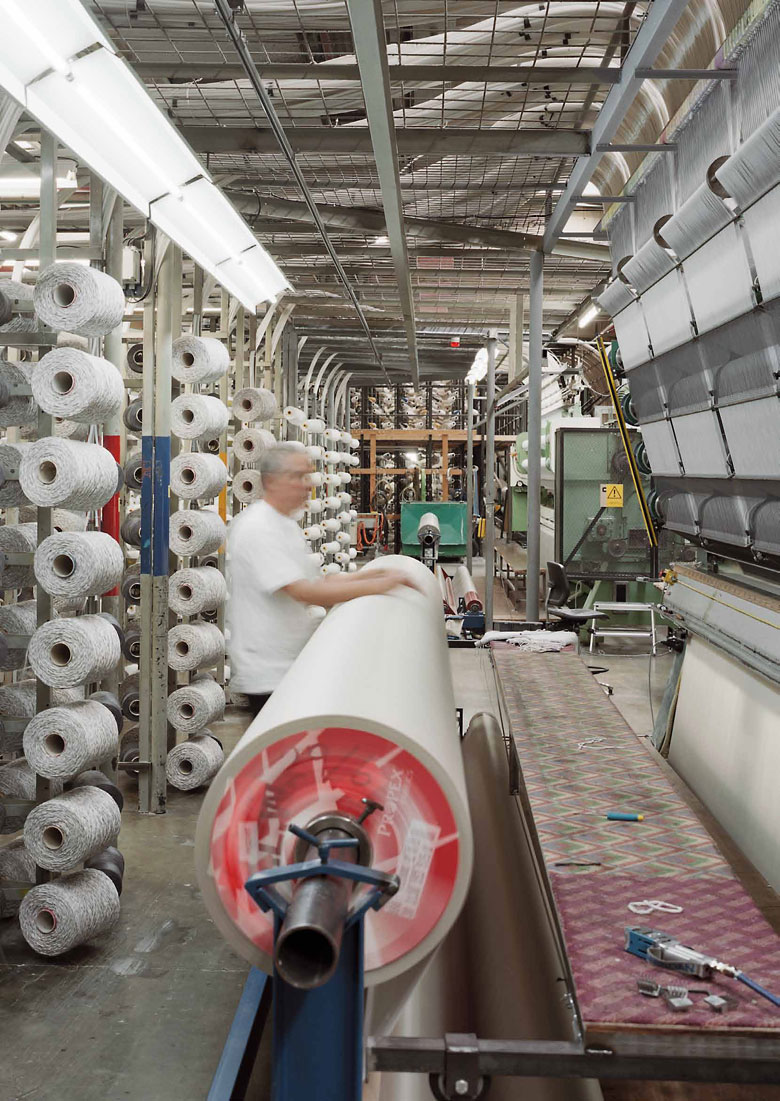
The white un-dyed yarn is sewn into a latex backing substrate in the Tufting department creating a dye-ready carpet 4 or 5 metres wide called ground tissue, which, for cut-pile carpets, is then tip-sheared to finish and even the surface and an anti-bleed treatment is added.
This ground tissue is then introduced to the Millitron, a sophisticated 120m long dye plant comprising 40,000 spray nozzles, similar to an ink-jet printer. Here the ground tissue is dyed in a computer controlled process.
The final process of the Millitron is the ‘hairdryer’ baking of any remaining dye to prevent blurring or bleeding of the design.
Once the dyed carpet exits the Millitron it is visually inspected for colour accuracy and quality assurance. Any imperfections in the dyeing process due to a nozzle head malfunction or blockage leaving an uncoloured stripe in the carpet will be later corrected by hand.

Each day the Millitron is set up with one of Ege’s four current standard colour scales (each scale consisting of 12 colours) and all the current product orders of that colour scale are fed through the machine to be coloured. For completely custom designs requiring a palette of non-standard colours normal production must be interrupted to equip the system with the correct colours, making completely custom designs very expensive.
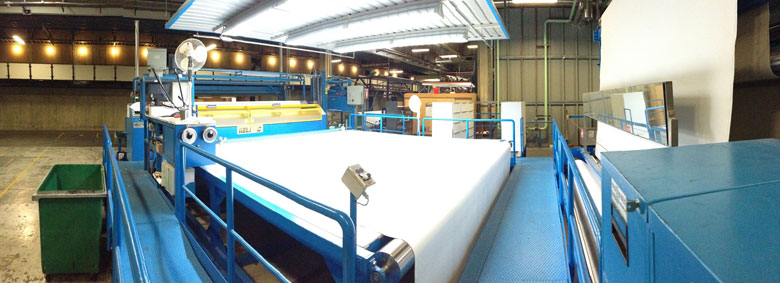
Ege also utilise a miniature dye machine that replicates the same process as the Millitron on a smaller scale to produce samples of custom colours and designs without interrupting the Millitron’s production.
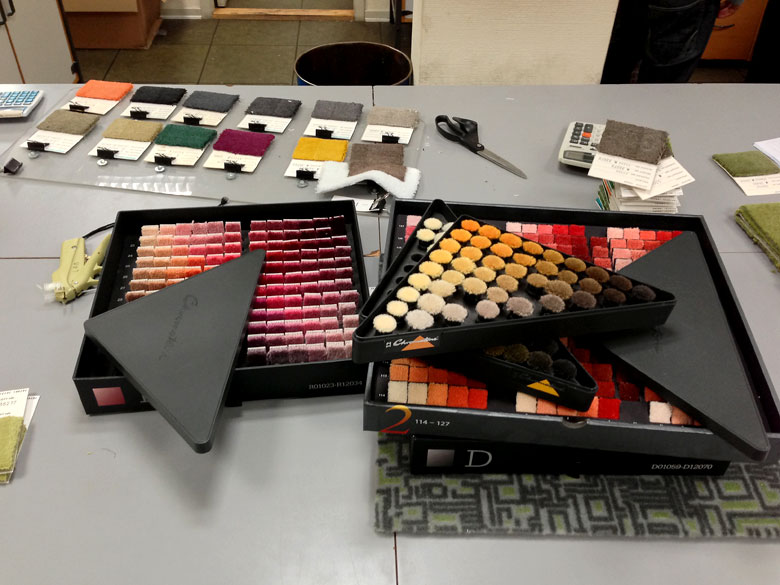
Hidden in the heart of the Millitron machinery is the dye lab. Here experienced colour specialists carry out the mixing and testing of the dyes to ensure the continued colour consistency of the standard colour scales and to colour match and mix new colours for custom designs.
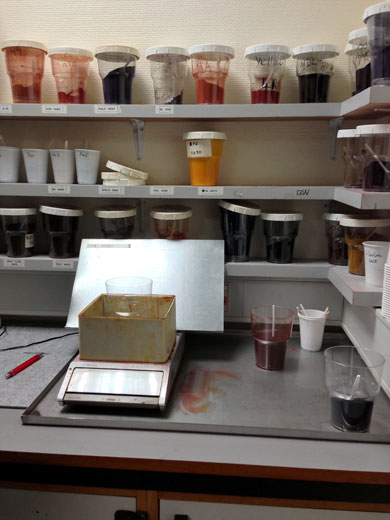
They are also responsible for ensuring the accurate reproduction of similar colours across the various yarn blends. As the amount of polyamide in a blended yarn increases the perceived colour of the dye changes, becoming more vibrant the greater the polyamide content is. By contrast, a pure wool carpet will have a less vibrant, warmer appearance. As a result not all colours can be replicated with complete accuracy across all yarn blends. A 100% wool carpet will never be able to replicate the more vibrant colours achievable on blends with a higher polyamide content.
This is a serious consideration to make if different carpet blends with the same colour palette are used in the same design scheme or environment (for example moving from a high traffic area to a low traffic area). Unless the dyes used for all carpet constructions are correctly colour matched so the desired colour is accurately represented on each blend then there will be a clear colour discrepancy as the flooring transitions from one construction to the next with a different polyamide content.
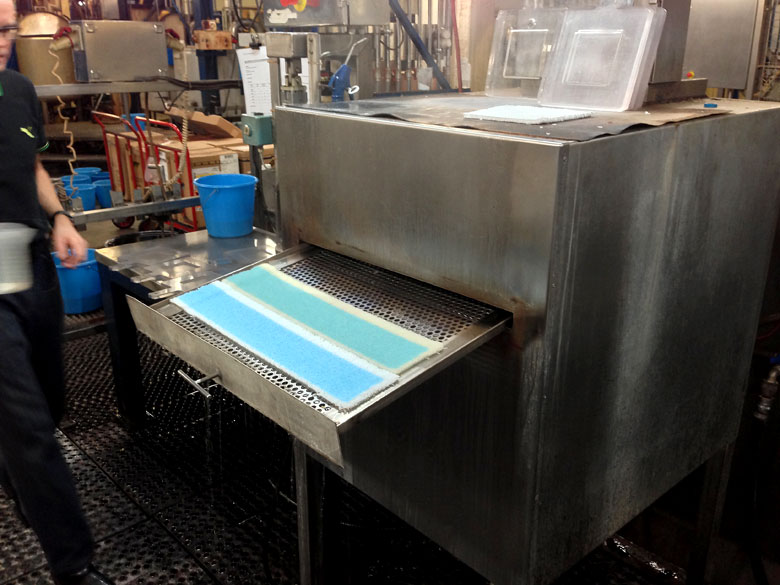
The workers here also evaluate and attempt to correct the discrepancy of colours when viewed under different light sources, a phenomenon known as Metamerism.
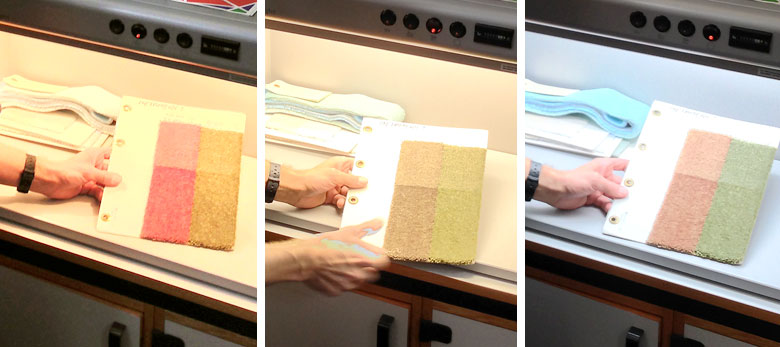
Using a colour assessment cabinet, which contains a range of bulbs imitating various light sources and temperatures (such as daylight, halogens and fluorescents), workers can view this affect and assess how it may affect the project and how it may be remedied.
Products:
• tufted carpet
• woven carpet
• carpet tiles
Material construction:
• high quality wool from New Zealand and UK
• ANTRON Polyamide
• backing made from latex, filler, auxiliary chemicals and textile backing
• dyes and chemicals including acid
Packaging:
• cardboard and plastic carpet tubes, wrapping foil and cardboard
Available formats:
• broad loom widths of 4m and 5m. Custom widths also available
• carpet tiles: 48 x 48 cm, or 96 x 96 cm

Applications:
• hospitality
• offices
• retail
• healthcare sector
• schools and institutions
• transport sector
• domestic (primarily Denmark and Sweden)
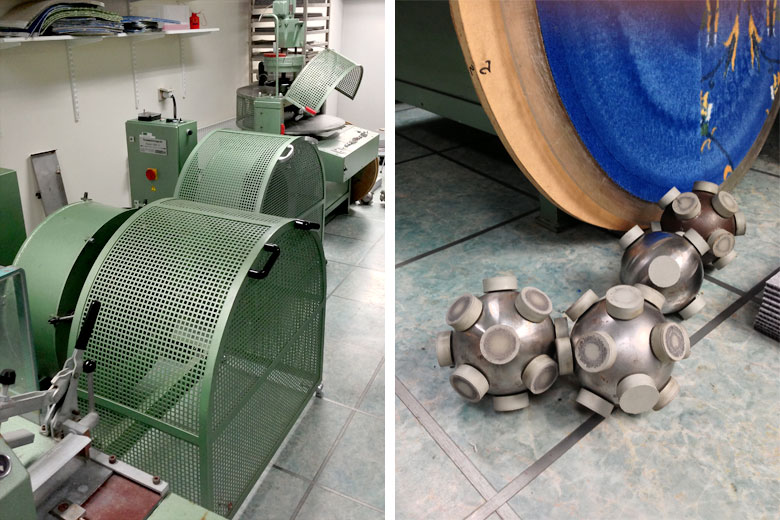
Testing:
Ege utilise an in-house testing facility for continuous product testing and quality control. For certification and classification, independent testing facilities are employed to ensure completely impartial testing and results.
Standards:
• EN 1307 – class 31-33
• EN 13501-1
• ISO 9001
• ISO 14001
• IMO certified
Performance notes:
• anti-microbial treatment available
• permanently antistatic
• wear rating: EN 1307 – class 31 moderate – 33 heavy duty commercial
• fire-resistance: EN 13501-1
Environmental considerations:
• textile floorings contribute to creating a healthier indoor climate
• halogen free, non-brominated fire retardant used in backing material
• all carpet tile backing is made of 100% recycled fibres
• in the Ecoline series 100% of the carpet fibres are recycled – a 50% reduction in the energy used in manufacture compared to producing new fibres
Water consumption:
• 6% of the total water consumption at Herning is recycled
• the dyeing works account for up to 79% of total water consumption
Energy consumption:
• since 1996, the combined heat and power plant at ege’s factory in Herning has generated electricity from natural gas, which is sold to the local power station
• natural gas is primarily used for heating of the backing furnace and the furnace for the carpet tile machine
• excess heat from electricity generation is used to produce steam for the Millitron dyeing system and for room heating
• the drying and vulcanising process requires high temperatures, for which energy consumption is high
CO2 emissions:
Since 2009 Ege have implemented a Greenhouse Gas Account to provide an overview and documentation of their CO2 emissions. A 39.5% reduction was achieved between 2009-2012)
Waste disposal:
• recovery – this includes the groups of waste from which it is possible to recover waste either for new production, or as a component in another product. Yarn and coil waste is recycled where possible
• thermal recycling – this includes yarn residues, cardboard bobbins, carpet residue, edge cuttings, sludge from the back coating line, and packaging that is not recyclable
• landfill – sludge from the cleaning and dyeing process, non-flammable waste and the waste that cannot be handled in the incineration plant is deposited in landfills
• destruction – waste for destruction includes waste oil, chemical and raw material residues, batteries and fluorescent tubes
Wastewater:
Internal wastewater purification is performed before discharge to the municipal purification plant.
Environmental accreditation and management:
• BRE Global listed
• Leed – individual carpet product specifications
• ISO 14001
• EMAS certificated
• DS/OHSAS 18001 – work environment management
• CE labelling
• BASTA registered
• INSTA 800
• Danish Indoor Climate Label
• Building product declarations available for some products
In their current environmental report, Ege outline their future plans for greater CO2 reduction, greater recovery during production, greater focus on cradle to cradle production and official certification (for selected carpet tile products) and greater promotion and investment in renewable energy. They have also begun to calculate the CO2 emissions related to the transport of their products from factory to the final destination.
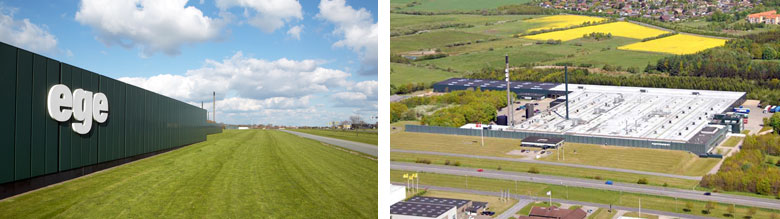